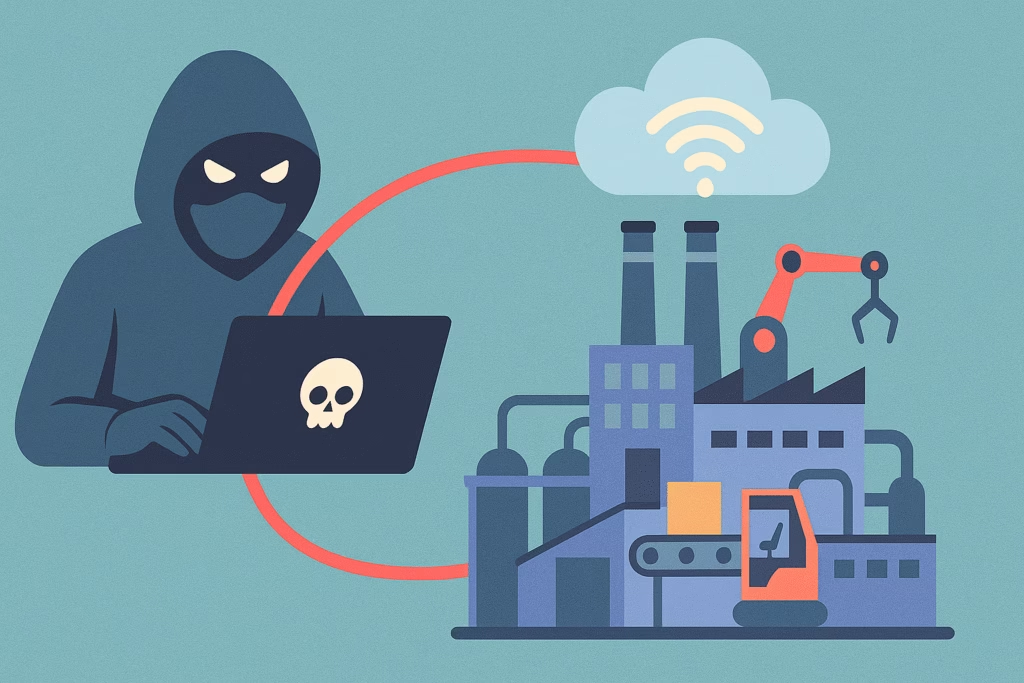
Smart factories represent the pinnacle of modern manufacturing efficiency, combining artificial intelligence, robotics, and interconnected systems to create unprecedented productivity gains. However, this technological revolution has inadvertently created a cybersecurity nightmare that keeps security professionals awake at night. The convergence of operational technology (OT) and information technology (IT) in industrial environments has opened new attack vectors that cybercriminals are eagerly exploiting.
The statistics paint a sobering picture: according to recent industry reports, cyberattacks on industrial control systems increased by 107% in 2023 alone. Manufacturing companies now face an average of 1,000 cyber incidents per week, with the potential for catastrophic operational shutdowns, safety hazards, and financial losses reaching millions of dollars.
The Evolution of Industrial IoT Security Threats
Traditional manufacturing environments operated in isolation, with air-gapped systems that provided inherent security through physical separation. Today’s smart factories have demolished these barriers, creating interconnected ecosystems where Industrial Internet of Things (IIoT) devices communicate seamlessly across networks. This connectivity, while enabling remarkable operational efficiencies, has fundamentally altered the threat landscape.
Modern smart factories typically contain thousands of connected devices, from sensors monitoring temperature and pressure to robotic arms executing precise manufacturing tasks. Each device represents a potential entry point for malicious actors. Unlike traditional IT environments, these industrial systems were designed for reliability and uptime, not security, making them particularly vulnerable to sophisticated attacks.
The Convergence Challenge
The merger of OT and IT systems has created unprecedented complexity in industrial cybersecurity. Operational technology, which includes programmable logic controllers (PLCs), supervisory control and data acquisition (SCADA) systems, and distributed control systems (DCS), was historically isolated from external networks. These systems prioritize availability and real-time performance over security, operating with minimal authentication mechanisms and limited encryption.
When these OT systems connect to corporate networks and cloud platforms, they inherit the vulnerabilities of both domains while introducing new risks specific to industrial environments. The result is a complex attack surface that requires specialized expertise to secure effectively.
Common Attack Vectors Targeting Smart Factories
Understanding how cybercriminals infiltrate smart factories is crucial for developing effective defense strategies. The most common attack vectors include:
Network-Based Attacks
Attackers often exploit poorly configured network segments to move laterally from IT systems into OT environments. Common techniques include:
- Network scanning and reconnaissance to identify vulnerable devices and services
- Protocol exploitation targeting industrial communication protocols like Modbus, DNP3, and EtherNet/IP
- Man-in-the-middle attacks intercepting communications between industrial devices
- Network segmentation bypass exploiting weak boundaries between IT and OT networks
Device-Level Vulnerabilities
IIoT devices often ship with default credentials, unpatched firmware, and minimal security features. Attackers exploit these weaknesses through:
- Default credential abuse using manufacturer-provided passwords that remain unchanged
- Firmware exploitation targeting known vulnerabilities in device software
- Physical access attacks compromising devices through direct manipulation
- Supply chain infiltration introducing malicious code during manufacturing or distribution
Social Engineering and Human Factors
Even the most sophisticated technical defenses can be circumvented through human manipulation. Industrial environments are particularly susceptible to:
- Spear phishing campaigns targeting operational personnel with industrial-specific lures
- Watering hole attacks compromising industry-specific websites and forums
- Insider threats exploiting privileged access from disgruntled employees or contractors
- Business email compromise targeting executives and procurement personnel
Real-World Consequences of Industrial Cyber Attacks
The impact of successful attacks on smart factories extends far beyond data breaches. Industrial cyber incidents can result in:
Operational Disruption
Manufacturing downtime costs can reach $50,000 per hour for automotive manufacturers and even higher for specialized industries. The 2021 attack on Colonial Pipeline demonstrated how cyber incidents can disrupt critical infrastructure nationwide, causing fuel shortages and economic ripple effects.
Safety Hazards
Industrial systems control physical processes that can pose significant safety risks if compromised. Attackers can manipulate pressure vessels, disable safety systems, or alter chemical processes, potentially causing injuries, fatalities, or environmental disasters.
Intellectual Property Theft
Smart factories generate vast amounts of sensitive data, including proprietary manufacturing processes, product designs, and operational intelligence. State-sponsored actors and industrial espionage groups actively target this information to gain competitive advantages.
Building Comprehensive OT Security Strategies
Protecting smart factories requires a multi-layered approach that addresses both technical vulnerabilities and human factors. Effective OT security strategies should include:
Network Segmentation and Zero Trust Architecture
Implementing robust network segmentation creates security boundaries that limit lateral movement and contain potential breaches. Key components include:
- Physical and logical separation between IT and OT networks
- Industrial demilitarized zones (DMZ) to control data flow between network segments
- Microsegmentation creating granular security zones around critical assets
- Zero trust principles requiring verification for every access request
Asset Discovery and Inventory Management
You cannot protect what you cannot see. Comprehensive asset discovery involves:
- Passive network monitoring to identify all connected devices and their communication patterns
- Asset classification based on criticality and risk exposure
- Vulnerability assessment of identified assets and their configurations
- Continuous monitoring for unauthorized devices and changes
Industrial Protocol Security
Securing industrial communication protocols requires specialized tools and expertise:
- Protocol inspection monitoring and analyzing industrial communications for anomalies
- Encryption implementation where supported by legacy systems
- Authentication mechanisms verifying device and user identities
- Protocol whitelisting allowing only authorized communications
Critical Infrastructure Protection Best Practices
Organizations operating smart factories should implement comprehensive security frameworks aligned with industry standards and regulations. The NIST Cybersecurity Framework provides an excellent foundation for industrial cybersecurity programs.
Incident Response Planning
Industrial cyber incidents require specialized response procedures that account for safety considerations and operational continuity:
- Safety-first protocols prioritizing human safety over system availability
- Isolation procedures for containing compromised systems without causing unsafe conditions
- Communication plans coordinating with regulatory authorities and emergency responders
- Recovery procedures restoring operations while maintaining security posture
Vendor and Supply Chain Security
Third-party vendors and suppliers introduce additional risks that must be managed through:
- Security requirements in vendor contracts and service level agreements
- Regular security assessments of vendor systems and practices
- Secure development practices for custom industrial applications
- Supply chain transparency understanding the origins and security posture of industrial components
Emerging Technologies and Future Threats
The industrial IoT security landscape continues evolving rapidly. Emerging technologies like 5G networks, edge computing, and artificial intelligence are creating new opportunities and challenges for smart factory security.
5G and Edge Computing Implications
The deployment of 5G networks in industrial environments enables new capabilities but also introduces additional attack vectors. Edge computing brings processing power closer to industrial devices, creating distributed security challenges that require innovative solutions.
AI-Powered Attacks and Defense
Artificial intelligence is transforming both offensive and defensive cybersecurity capabilities. While AI can enhance threat detection and response, it also enables more sophisticated attacks that can adapt to defensive measures in real-time.
Regulatory Compliance and Industry Standards
Smart factories must navigate an increasingly complex regulatory landscape. Key compliance frameworks include:
- NERC CIP for electric utilities and power generation facilities
- TSA Pipeline Security Directives for oil and gas pipeline operators
- FDA cybersecurity guidance for medical device manufacturers
- IEC 62443 industrial automation and control systems security standards
Building a Security-First Culture
Technology alone cannot solve industrial cybersecurity challenges. Organizations must foster a security-aware culture that empowers employees to identify and report potential threats. This includes regular training on phishing awareness, as social engineering attacks often serve as the initial entry point for more sophisticated industrial cyber attacks.
Services like PhishDef can play a crucial role in educating industrial personnel about phishing threats and building organizational resilience against social engineering attacks that target operational technology environments.
Key Takeaways for Smart Factory Security
Securing smart factories requires a comprehensive approach that addresses the unique challenges of industrial environments:
- Recognize the expanded attack surface created by IIoT device proliferation and IT/OT convergence
- Implement defense-in-depth strategies combining network segmentation, asset management, and protocol security
- Prioritize safety considerations in all security decisions and incident response procedures
- Address human factors through comprehensive security awareness training and phishing protection
- Stay informed about emerging threats and evolving regulatory requirements
The transformation of manufacturing through smart factory technologies offers tremendous benefits, but it requires organizations to fundamentally rethink their approach to cybersecurity. By understanding the threats, implementing comprehensive security strategies, and fostering a security-first culture, manufacturers can harness the power of industrial IoT while protecting their operations, employees, and competitive advantages.